[ad_1]
Uncover how real-time information and streamlined processes can improve what you are promoting operations. Study confirmed methodologies to attain operational excellence, minimise waste, and ship superior buyer energy.
Many challenges exist in as we speak’s fast-paced and extremely aggressive enterprise setting, resembling speedy technological developments, information safety and privateness, evolving buyer developments, digital transformation, and evolving buyer developments.
Operational excellence has change into a vital differentiator for organisations striving to thrive and keep forward of the competitors. These methods assist streamline processes, optimise effectivity, and foster a tradition of steady enchancment.
You’ll be able to improve productiveness, minimise prices, and ship distinctive worth to your prospects by reaching it.
This complete roadmap discusses enterprise excellence and a few methods to empower your organisation and show you how to thrive in as we speak’s aggressive panorama.
What’s operational excellence?
Whereas each firm runs its enterprise in another way, a number of components, resembling enterprise methods and buyer expertise, have to be thought of.
This strategic method focuses on steady enchancment and optimisation of enterprise processes to attain higher outcomes. It seeks to minimise waste, improve productiveness, and align assets with what you are promoting targets.
Organisations should sustain and bear an end-to-end enterprise transformation in as we speak’s quickly rising and technology-based enterprise panorama. In any other case, they’ll be left behind by their competitors.
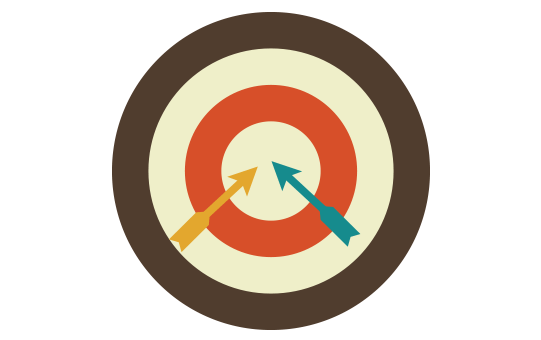
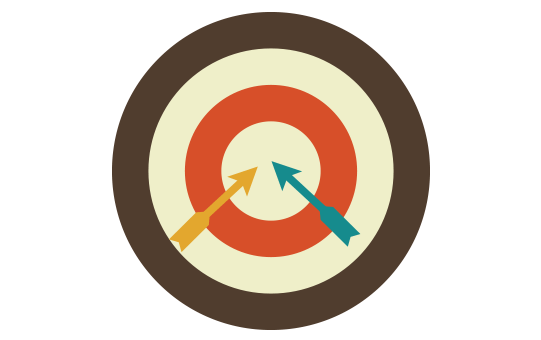
Enhance your worker engagement in lower than two minutes
Get began without spending a dime as we speak.
This enterprise technique just isn’t a one-time endeavour however somewhat an ongoing journey of steady enchancment.
Nevertheless, earlier than embarking on this journey, organisations should clearly perceive their targets, present processes, efficiency metrics, and areas for enchancment.
Are operational excellence and steady enchancment the identical?
Whereas the 2 are interconnected ideas with a symbiotic relationship, they’ve key variations.
- Scope: The scope of the previous is broader and extra holistic, whereas the latter is targeted on making incremental enhancements.
- Length: Operational effectivity is a long-term initiative, whereas steady enchancment, from the identify itself, is an ongoing course of.
- Focus: The previous optimises all elements of what you are promoting operations, and the latter makes small enhancements to particular areas.
- Mindset: Enterprise excellence embraces effectivity and effectiveness, whereas steady enchancment welcomes fixed studying and making gradual progress.
An organisation should undertake steady enchancment to achieve enterprise excellence. In spite of everything, you’ll be able to at all times discover methods to refine operations.
The one option to go is up, and even when you’ve reached the summit and showcased your full potential, you will need to know how one can preserve that peak efficiency.
Each ideas are vital in enhancing an organisation’s sustainability and competitiveness whereas fostering a tradition of innovation and effectivity.
Why is operational excellence essential?
One of many vital methods enterprise excellence issues to what you are promoting is it streamlines workflows and removes disorganisation, leading to higher decision-making expertise.
With information analytics and key efficiency indicators (KPI) to trace efficiency, you’ll be able to higher determine developments and perceive buyer behaviour. Minimise dangers as a consequence of incomplete info and make factual and evidence-based selections somewhat than intestine really feel or instinct.
Operational effectivity lets you determine issues that aren’t working effectively and know what modifications have to be made. You develop a eager mindset and a way of agility, particularly in quickly altering enterprise landscapes.
Furthermore, adapting a strategic method lets you meet your buyer’s wants higher and ship distinctive worth. This method lets you optimise processes, foster a customer-centric tradition, and leverage data-driven information insights.
Lastly, operations administration enables you to foster a thriving firm tradition and push for a system improve. Stray from damaged processes and failed frameworks and concentrate on constructing an organisation based on steady enchancment, worker empowerment, and customer-centricity.
Constructing a constructive and dynamic work setting makes workers really feel engaged, motivated, aligned with the corporate’s targets, and, extra importantly, valued.
Reaching enterprise excellence with Shingo Mannequin
The Shingo Mannequin, generally known as the Shingo Prize for Operational Excellence, is a framework for constructing sustainable organisational excellence.
The Shingo Institute, a part of the Jon M. Huntsman Faculty of Enterprise at Utah State College, developed it. It was modelled after Dr. Shigeo Shingo, a Japanese industrial engineer and a key contributor to the event of the Toyota Manufacturing System.
This mannequin emphasises the significance of how and why operational effectivity is achieved. With Shingo Mannequin, you break down every system into smaller elements, providing you with a deeper understanding of the correct KPIs and indicators to measure success.
The Shingo Mannequin has ten core rules divided into 4 classes: Cultural Enablers, Steady Enchancment, Enterprise Alignment, and Outcomes. Notice {that a} precept in a single class might interlap with others.
Cultural enablers
That is targeted on making a firm tradition that fosters steady studying and excellence. It recognises that enterprise tradition is essential in shaping how workers suppose, behave, and method their work, finally influencing the organisation’s general success.
As an illustration, the “respect each particular person” precept teaches each particular person throughout the organisation should worth each other, no matter their position or place.
In the meantime, “lead with humility” lets leaders embrace modesty and be open to suggestions. Furthermore, “search perfection” units excessive requirements for efficiency and strives for excellence.
Steady enchancment
This class is targeted on bettering the move of data from one division to a different and constantly in search of methods to enhance enterprise operations. It centres on long-term targets and strives to good processes.
“Embrace scientific considering” is a option to observe this class, which bases selections on information and proof derived from scientific strategies. It additionally helps to “concentrate on the method” somewhat than solely take note of outcomes.
Whenever you “guarantee high quality on the supply,” good high quality is achieved the primary time, and may an error happen, it’s greatest whether it is detected and corrected when it’s created.
Enterprise Alignment
This class ensures the whole organisation is aligned in the direction of a standard function and aim.
With this class, each division and performance have to be coherent and synchronised to attain enterprise excellence. It additionally addresses the worth of making a unified imaginative and prescient and a tradition supporting the corporate’s targets.
It helps to “create fidelity of function” and align all efforts in the direction of a standard mission. Staff who embrace your aim usually tend to be dedicated to reaching it.
You must also “create worth for the client” by trying by way of a shopper’s perspective. Doing so lets you realize what they need, encourages you to “suppose systemically”, and discover methods to create higher worth for them.
Outcomes
When you’ve carried out the above-mentioned classes and their rules, you measure their outcomes and impacts on the organisation. The Outcomes class evaluates the tangible and intangible results that your organization has achieved, reflecting the effectiveness of your efforts, efficiency enhancements, and drive for fulfillment.
One of many key indicators of success and sustainability is the way you “create worth for the client.” In spite of everything, the aim is to satisfy their expectations. You measure buyer satisfaction and attempt to maintain this degree of enterprise excellence.
Reaching enterprise excellence with Lean Manufacturing
This systemic method goals to get rid of waste and maximise effectivity in manufacturing processes.
A lot of its traits are carefully associated to the Shingo Mannequin however have been first utilized within the automotive manufacturing course of, particularly by the Toyota Manufacturing System (TPS) within the Nineteen Fifties. Since then, many industries have adopted this method.
Lean Manufacturing has 5 core rules: worth, worth stream mapping, move, pull, and perfection.
Worth
Worth refers to a shopper’s perspective and the way a lot they’re keen to pay on your services and products. It emphasises the significance of understanding their wants and preferences to create one thing invaluable.
Whenever you prioritise worth, you exert effort on actions that actually matter to prospects, lowering waste and enhancing buyer satisfaction.
Worth stream mapping
This precept maps out the whole manufacturing course of from begin to end, analysing the assets required to provide a services or products. It identifies areas of waste and inefficiency, analyzing something that doesn’t add worth and discovering methods for enchancment.
Circulation
Disharmonious manufacturing processes incur prices, delays, and waste. Creating move means lowering bottlenecks and different obstacles that create waste and sluggish manufacturing. It ensures a easy course of for improved lead instances.
Pull
Pull is an idea that optimises workflow and supplies all through the worth stream. In contrast to conventional “push” methods forecasts drive manufacturing, a Pull system is pushed by precise buyer demand. Inaccurate forecasts create waste, as an excessive amount of or inadequate product is produced to satisfy demand.
Perfection
Perfection refers back to the relentless pursuit of excellence and steady enchancment in all elements of an organisation, from processes to services and products.
It’s primarily based on the understanding that there’s at all times room for enchancment and that no course of or system is ideal. You obtain larger efficiency ranges when you decide to this ongoing journey of eliminating waste and inefficiencies.
Reaching enterprise excellence with Kaizen
This subsequent methodology is of Japanese phrase that may be damaged into two elements: “kai,” which suggests change, and “zen,” which suggests good or for the higher. Due to this fact, it basically interprets to “change for the higher.”
Just like steady enchancment, Kaizen focuses on enhancing processes and methods by way of small and incremental modifications over time. It believes each course of, product, or service inside an organisation can get a system improve, no matter how environment friendly it could appear. The first aim is to spice up effectivity, high quality, and general efficiency by involving each workforce member within the enchancment course of.
Right here’s an instance of information questions with steady enchancment initiatives in thoughts. It’s a continuous course of that goes again to the start because it retains on discovering areas of enchancment.
- What’s the root reason behind the issue?
- How can it’s addressed?
- Are the modifications carried out persistently, by everybody, and in all areas?
- What impression do these efforts create?
- How else can we hold bettering?
The core rules of Kaizen
Like Lean Manufacturing and the Shingo mannequin, Kaizen rests on varied basic rules.
Know your buyer
Kaizen encourages organisations to have a customer-centric focus the place all enhancements are achieved to learn the client finally. There are numerous methods to worth prospects and improve their expertise, resembling offering higher services and products, shortening lead instances, and bettering satisfaction.
Let it move
Kaizen additional goals to attain zero waste or uncooked supplies, motion, and time used to perform a activity. Whereas it could seem to be an not possible aim, this technique goals to enhance constantly. By letting it move, each particular person within the organisation works towards eradicating any waste from their space.
Go to Gemba
Gemba is derived from the time period gemba or gembutsu, which accurately interprets to “the actual place.” It encourages leaders to find out how a particular course of works and know what truly occurs at each degree of the organisation. It additionally pushes for gaining insights from each workforce member. Kaizen urges to observe the motion, as worth is created the place one thing is occurring.
There are three parts to an efficient Gemba Stroll.
- Go See: As leaders immerse themselves in each degree of the organisation and observe the method, they get an concept if every thing is completed in line with requirements and if meant outcomes are produced. It’s greatest to plot a guidelines to maximise the Gemba Stroll.
- Ask Why: The aim of a Gemba Stroll is to study by probing the worth stream, determine alternatives for system enchancment, and talk and pay attention actively to each member. Leaders ought to present sincerity about an worker’s work and solicit suggestions and solutions to enhance it.
- Present Respect: Gemba Stroll focuses on the organisation’s challenges, not the worker’s efficiency. It’s the good alternative to know these considerations and decide how they are often addressed.
Be clear
Having information is a measure for fulfillment, permitting you to trace efficiency and enchancment. It additionally enables you to resolve the place and how one can refine the system. The outcomes you want to obtain have to be measurable and tangible. Other than measuring progress, organisations can use this info to determine areas for enchancment and set efficiency targets.
Empower individuals
Leaders should set uniform targets for all workforce members and be given the instruments, processes, and methods wanted to attain them.
In Abstract
Unleash operational excellence with the ability of those totally different methodologies. Improve buyer satisfaction, streamline operations, and drive steady enchancment to maintain up with as we speak’s aggressive panorama.
Concerning the Writer
Anna Marie Martinez has been writing professionally since 2018, protecting varied purchasers like journey, chiropractic, canine well being, inside design, digital advertising and marketing, and extra. She is a full-time internet content material author for Utak POS for nearly three years.
[ad_2]